
Pharmaceutical compliance issues and observations have been at an all-time high in recent years. However, the best time to comply with all quality policies is before any problems or warnings arise.
Common FDA Compliance Issues
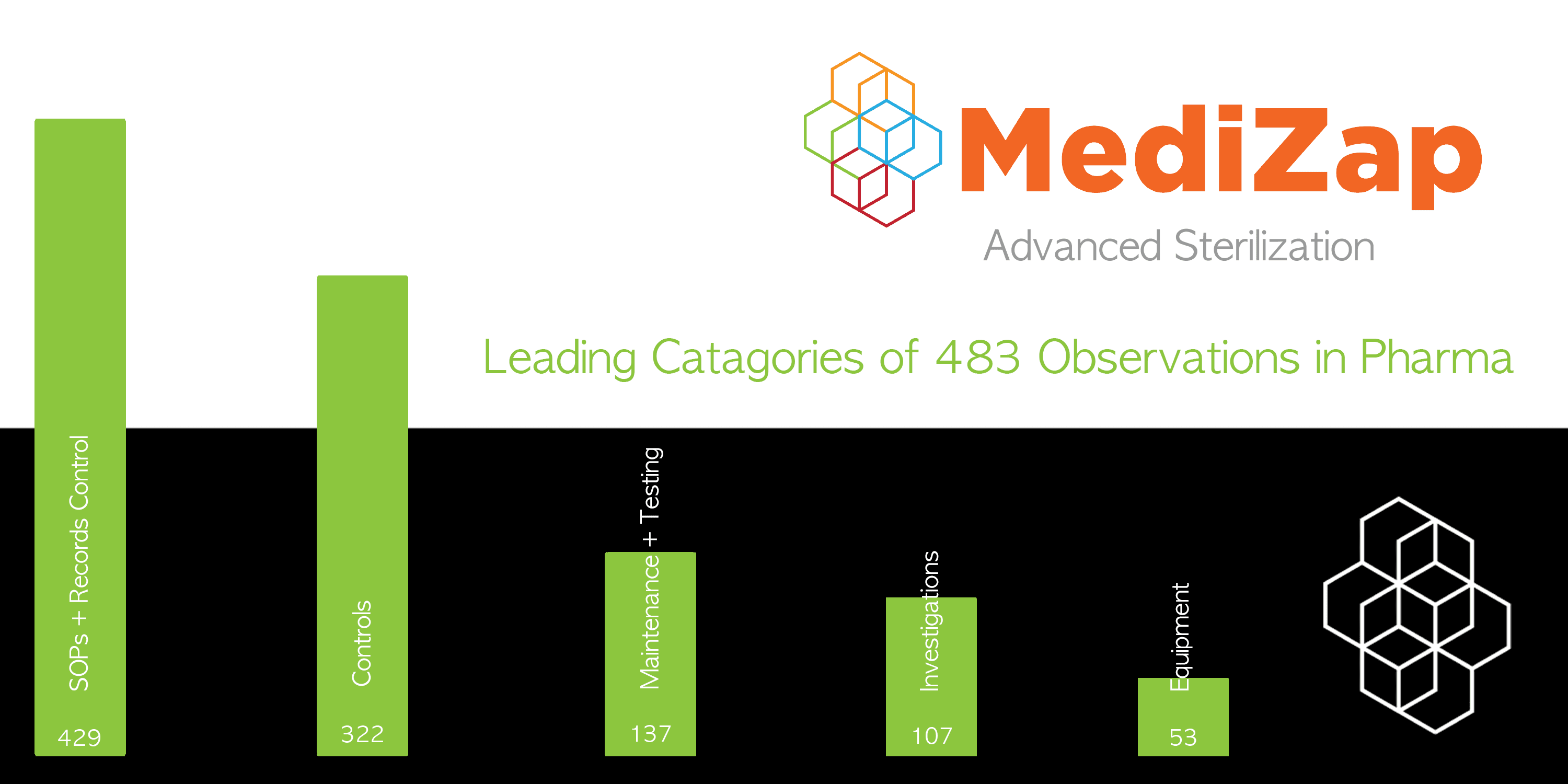
- Lack of Written Procedures or Failure to Follow Written Procedures
Citations in this category have increased year over year due to regulators’ increased focus on this issue. Effectively documenting processes that are simple to implement and perform can be a challenge but maintaining clear and consistent SOPs can lower these procedural issues. Specifically, ensure that employees collaborate and understand their roles and responsibilities through clear formatting and language in guidelines.
- Failures in Laboratory Controls
Proper laboratory controls provide accurate data. Good compliance for laboratory controls includes scientifically appropriate testing procedures and standards, the monitoring of accuracy and precision of techniques and instruments, and the identification and handling of testing samples.
When an inspector from the FDA reviews laboratory controls, they focus on lab operations and raw data. Therefore, inspectors will typically review records and logs, SOPs, analytical procedures, lab data, and equipment. To avoid these compliance issues, ensure proper management of data, adherence to SOPs, and instrument calibration.
- Faulty Production Record Reviews
The Code of Federal Regulations (CFR) states that all quality control must be done by the pharma QC unit and approve all production and control records. If there are any discrepancies, a thorough investigation must be completed, and follow-up actions must be assigned. A failure to review all logs (including downtime, cleaning, and clearance), procedural shortcomings, or a lack of shared procedures are ways to cause this citation.
The QC team needs to have unified standards and SOPs for record review to ensure all records are reviewed within proper parameters to avoid these issues.
- Absence of Written Procedures
A lack of written procedure for process and production controls is a necessity to remain in proper compliance. Therefore, the FDA requires that all pharmaceutical organizations create documented production and process control procedures, including SOPs for drug identity, strength, quality, and purity. Ways to be out of compliance include a total lack of appropriate methods, documented instances of SOP failures, non-approved processes, and no training records.
Most of these issues can be corrected with proper transparency and workflows within the organization.
No company wants its first interaction with the FDA to result in a dreaded 483 letter. But, unfortunately, receiving one of these letters is a sign that processes and documentation are being overlooked and can be detrimental to the overall safety of pharmaceutical components.